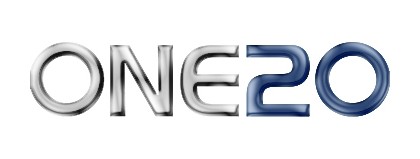
We have a unique way of working with our clients. We are a solutions provider, so much more than just being a supplier of architecture and design services. We like to work alongside our clients and other design professionals. This collaborative business culture is geared to smarter ways of operating, enabling us to achieve high standards of delivery and performance within budget and time constraints.
Sustainability is a core component of all our work. Our award winning architects look to maximise the opportunities that a site reveals. This results in buildings that comprise creative environmental, space or cost saving solutions.Epoch Institute – Sustainable Carbon Neutral Fitout
Sustainable Carbon Neutral Fitout
This project recently won the runners up prize in the Victorian Premier’s Sustainability Awards 2022!
We successfully produced a healthy office fitout with a Carbon neutral result.
This project is unique in the width of its scope across a small office fitout. Its sustainable initiatives stretch across the stages of design, construction and day to day work practices. This has arisen from a collaborative approach between the client, builder and architect.
The existing office space was the opposite of sustainable. It was a dark soulless space with no windows and hence no natural light or ventilation, relying instead on energy sapping halogen lighting.
The Epoch office is an institute that was launched in 2020 and its goal is to reimagine people, place and planet. Its specific mission is to inspire and educate businesses and communities to adopt environmentally conscious values so that both people and nature can thrive into the future. It is a co-working space, a think tank and a boutique conference facility that is unique in Australia.
This project is an exemplar in reusing waste in the construction industry. 46% of Landfill in Australia is construction waste. This project eliminated waste wherever possible along all lines of the construction chain. The aims of the project were
1. Increase the re-use of construction waste
2. Enhance total life cycle energy efficiency in the building
3. Substituting non-renewable energy sources for renewable ones
4. Increased control over pollution via low-VOC materials, natural ventilation and biophilia
5. Building for longer lifespans and reusing/recycling
6. Take advantage of sustainable passive design principles
7. Produce a space for further community engagement
Through the creation of the new space, we aim to inspire and educate individuals, organisations, communities, businesses and governments to adopt new ways of thinking and new technologies around construction, placemaking, collaborative systems and ethical behaviours. It was essential that the space itself was created through the commitment to sustainable principles by all the contributors.
The building is in a mixed use community. The barriers included heritage overlays, neighbourhood engagement and the fire/structural risks that come with a historic building. We began this project committed to the underlying principles of a just, regenerative and compassionate world. Sustainability informs all decisions. Whenever we have had to deal with challenges, we aim to do that consciously, with care and with the understanding that such small decisions are foundational.
The design of the building introduced natural light and ventilation. Planter beds were coupled with views out to the historic tree and courtyard. Passive environmental principles were incorporated. All fixtures and finishes were chosen for their environmental advantages.
Construction involved collaborating with builder Gypco to develop a no-waste construction strategy. We dramatically reduced the carbon and environmental footprint. The project created its own momentum starting with no single-use cups on site and provision of coffee cups made from corn starch. This was the commitment evident at every step.
Construction waste was kept to a bare minimum, by reusing cut-outs of plasterboard, involving over 200 patches meaning no new plasterboard was neither needed nor old plaster sent to land-fill. The existing carpet was sent to be recycled and timber salvaged from other Gypco projects was used to complete the fitout.
We recycled 4146.2kg plaster, 1241.6kg of mixed timbers and 2824kg of mixed metals, which otherwise would have been landfill also producing GHG emissions via transportation. If the timber were to breakdown in landfill, methane would have been released, a greenhouse gas roughly 25x more potent that carbon dioxide. The materials have been given a second life to be used again, having a lower carbon footprint than manufacturing the products from virgin materials.
The project introduced sustainable interventions at each stage.
DESIGN STAGE
-Designing a new balcony, windows and planters to bring in natural light and provide wide views to sky and courtyard
- Specifying Carbon Neutral Carpet and Greenstar rated rubber from Interface
- Specified Low-e thermally broken double glazing
- Design openable louvres to bring in natural light and ventilation and draw scent from planter beds foliage into the interior
- Use of Biophilia inside and out, generating interactions with nature,
- Specifying easily cleanable materials
- Specifying Low VOC material for new joinery.
- Design fire screening to windows to be used as sun shading
- Specifying Use of FSC certified Timber
- Introducing Accessibility modifications
- New planting reduces inner city heat island
- Improving light quality, reducing power consumption and limiting light wastage/ pollution are key objectives of the FOS Lighting. Lighting design phase that emphasizes the effectiveness of solutions and the use of recyclable building materials.
CONSTRUCTION STAGE
- Near total elimination of construction waste through recycling, re-using and repurposing.
- Replacement of Halogen lighting with energy efficient LED lighting manufactured in Australia by a local Richmond firm, FOS. Use of High CRI, good durability, low consumption lighting controllable by user. Good contrast between wall floor and ceiling aid accessibility.
- Reusing plasterboard cut-outs of ceiling and walls meant no new plaster was used or old plaster needed to be disposed of.
- Elimination of single use plastic and coffee cups on site. Provision of corn starch cups to every worker and visitor.
- Prevention of pollution and emission reduction during construction via construction air quality management policies
- Re-use of FSC certified Timber and salvaged building materials from other Gypco project sites
- Minimising demolition and prioritising reuse of any demolition material. Re-use of historic building .The most sustainable piece of building is the building you do not have to do.
- Use of Low VOC chemical free water based Eco paint and recycling leftover paint at end of project
- Low emitting materials in flooring adhesives insulation and sealants
- Old demolished carpet and lighting sent to recyclers
OPERATION STAGE
- Use of second hand furniture and locally produced materials
- Reduction of harmful materials and sources of mercury, lead, cadmium copper and asbestos.
- Institute solar power generation as a whole of building operation for café, residences and offices
- Rainfall collection
- AC overflows to water plants
- Use of Energy efficient and water efficient appliances and water saving taps and toilets
-Bicycle parking and change/shower facilities
- Electric charge station
- Recycling and waste management practices
- Provision of sustainable work practices during operation including nutrition, exercise, organisational transparency, and cleaning and maintenance procedures
FOS lighting has End of its life, where materials are collected and disposed of adequately.
-End of life carpet recycling policy adhered to by Interface
- Builders planting trees in Daintree to offset carbon footprint
- Architects and clients donated use of 55Ha land to environmental charity Greenfleet to plant native forest and carbon credits.
We used Noraplan rubber flooring from Interface. This flooring received a Level A Green rate from GreenTag. It has a Greenstar Design and Built v1.1 and Interiors v1.1 Rating tool credits for sustainable products and Indoor pollutants as well as a Greenstar Performance v1.1 rating tool credit for Procurement and purchasing and refurbishment of materials and additionally Greenstar legacy tools credits for Mat flooring IEQ volatile organic compounds (VOC)
The Composure carpet, also from Interface received an environmental certificate from the ACCS scheme. They are manufactured in Australia reducing transport pollution costs. All products are manufactured locally at Minto and meet Australian Carpet Classification Scheme standards and are certified and recognised by the GBCA Green Star rating system.
The GYPCO team constructed each planter box from entirely upcycled materials. 22kg of steel, 14kg timber, 13kg cement sheeting, 1L LOW VOC black paint and 2kg of corflute were used. This has saved minimum 100 kg CO2e in emissions from using virgin materials, equivalent to driving 400km.
A total of 9488.31kg of construction materials were upcycled and recycled upon completion of the build. All materials used had a total embodied carbon of 9396.67kg carbon dioxide equivalent (CO2e-). Considering these materials were upcycled, the processes that create the embodied carbon in those materials become negligible. By recycling materials, the emissions from materials breaking down in landfill are avoided. Approximately 9396.67kg of CO2e- was saved from being released into the atmosphere, which would have occurred in typical cases, when clients and builders aren’t eco-conscious and choose to use virgin materials, and discard materials to landfill. The majority of materials by weight were recycled, meaning if they had been landfilled as in the majority of renovations, this would have released GHGs into the atmosphere as the materials degraded over time.
The key innovation was to create a healthy building and retrofit a heritage floor that minimises the carbon footprint by upcycling all rubbish and building materials and recycling and reusing timbers. There were many behaviour changes to traditional practices. Epoch are now a green office, they avoid the use of single use plastics and recycled paper wherever possible. They have installed an electric charging station and bicycles racks to encourage workers to take more sustainable modes of transportation.
Whist it is a carefully and beautifully crafted fitout, its appearance is almost immaterial. The fact that the clients have opted for second-hand furniture is testament to their commitment to the higher environmental principles. At just $147,000 over an area of 240 msq, the fitout also proved that it does not cost the earth to incorporate sustainable design. It might even save it.
Over 340L of eco-paint (no chemicals) was used, and 29L of this was upcycled upon completion. By upcycling and recycling materials, in combination with sustainable on-site behaviours and tree planting, this project offset its carbon footprint. The project was net carbon negative due to the additional tree planting drawing down more carbon than what is being released into the atmosphere.
Biophilia was introduced into the space in terms of internal and external planter beds. These in term also bring natural light, fresh air and the scents of fresh native flora into the work-space. Fire protection screens triply also act as sunshading and trellising.
The overflow from the air-conditioning systems were redirected to the planter beds. A simple measure that means when it is hot and dry the plants receive extra water.
All clients should follow this inspiring lead and strive to achieve carbon negative builds so we can reverse current detrimental planetary impacts.
The project is environmentally sustainable over its long term future. The project has demonstrated that building waste can be greatly reduced during the construction phase. It does not end there with the end life of materials considered beyond the tenancy period.
Carpets and other finishes are recyclable and re-usable. Interface claim that “All carpet at end of life is taken back by Interface Australia under its product stewardship program – ReEntry. ReEntry is a true a circular economy model that allows Interface retain value in the supply chain by recycling the product at end of life. The recycling installation at Minto was commissioned in 2017 to reprocess Interface post-consumer carpet from the Australian market. Interface has reduced the carbon footprint of its products by 76% and all products are now carbon neutral across their full life cycle which includes the operational emissions associated with the use phase of the carpet’s life.”
The use of Low VOC Eco paint and joinery coupled with the introduction of fresh air and internal Biophilia increases the long term health of the inhabitants. Low–e thermally-separated double glazing ensures energy costs will be lower over the life of the building. Natural lighting reduces the reliance on artificial lighting, which is now LED. Energy efficient appliances add to the longevity. Water saving toilets and taps ensure water use is kept to a minimum.
The clients and architects have looked beyond the inner city site and have donated the use of 44 hectares of land and its associated carbon credits they jointly own in Tumbarumba NSW for the use of the environmental charity Greenfleet to plant Native forest. This will more than offset any carbon footprint produced by the office building workers and the architectural staff over the minimum 30 year life of the forest scheme.
This project provides an exemplar of how architects, builders and clients can work together to create a sustainable building process and reduce waste. By making the simple decision to choose upcycled materials and recycle unusable materials we have saved GHGs from entering the atmosphere, and further contribute to climate change which is already occurring at an unpresented rate. To draw a comparison, we have chosen to not drive around Australia 3 and half times, or fly a Boeing 747 plane for 37 hours.
To offset their small carbon footprint, the GYPCO construction workers planted 115 trees in the Daintree. These trees will draw down ~10,005kg CO2e- over 100 years. This is the same as drawing down the emissions created from driving a medium sized vehicle 40,024km. This tree planting will more than comfortably offset the carbon footprint of the behaviours of the construction staff over the course of the project.
The business plan for the Epoch Institute itself sets a clear direction for the organisation and its collaborators, consistent with the needs of the urgent climate change induced time we are in globally. Future benefits are multiple; one is the benefit to the community. People will be trained up within a sustainable building to become placemakers with emotional intelligence
As an organisation Epoch will continue to engage with the community through their website, free talks, working in grief and empowerment counselling and teaming up with multiple organisations. The initiative will expand in the future by making Epoch a local and global centre for placemaking and localisation, resilience and regenerative systems. It will also act as a community based building focused on the adoption of deep ethical sustainability values.
We would hope that all architects, builders and clients could follow this excellent example of building production.